Knowledge, experience, involvement.
Our realizations.
Our work
Many years of experience of our specialists in performing tasks in the field of automation and industrial IT resulted in solutions that we have successfully implemented at out Customers'. These solutions, many times, allowed a great improvement of a machine or a production line and optimization of production costs. Here are some examples from the past couple of years:
Control system and increase in effectiveness
One of our Customers had a large difference in the productivity of the production line on night and day shifts. The reason for this was unusually large number of stops during night shift. However, it was not known what caused the shutdowns. One of the first ideas of the Client to solve the problem was the installation of cameras recording the line work, which unfortunately did not give any effect.
The Customer turned to us for help. After a thorough discussion about the problem and the characteristic of the production line, our specialists developed a system in which the operator had to state the reason for stopping the line to resume production. The Customer also received a security key to bypass the system in the event of a failure of the system recording the reasons for stopping the machine. The solution proved to be reliable enough that no service is required, and any changes or improvements can be made on a day-to-day basis through remote management.
As a result, the productivity of the production line increased from 48% to 72%, and the number of unnecessary line stops decreased to the necessary minimum (planned stops and damages to the machine). Our system allowed the Customer to gain clear control over the production process while improving efficiency.
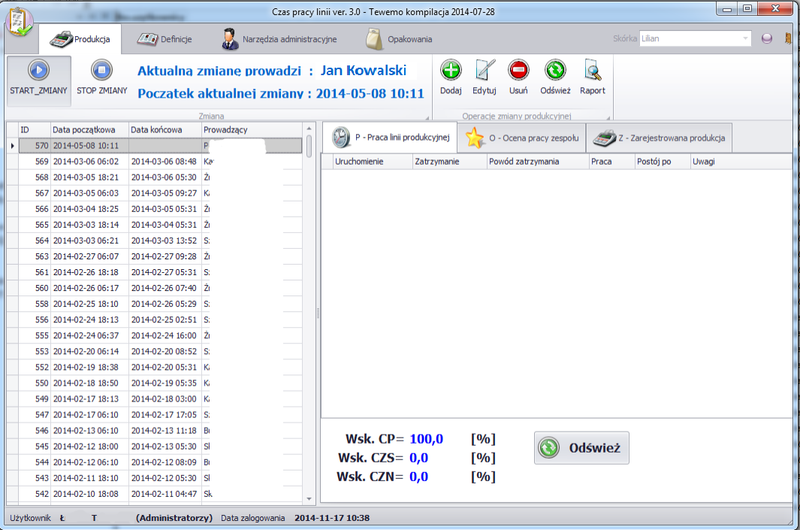
Effective combination of technological knowledge with the control system
One of the Customers owns a machine for the production of specialized liquid (both the machine and the liquid production technology are the secret of the customer). The method of production of this liquid requires the exact implementation of subsequent stages of its production, while maintaining production parameters such as temperature or pressure. This knowledge was owned by only one of the specialists of the company and only he was able to produce the liquid meeting all the required properties of the end product.
After a few conversations between Tewemo specialists and the Customer's technology engineer, a control algorithm was developed. It met the needed criteria of the control – the stages of liquid production while maintaining production parameters.
The rewritten control program and visualization of the machine's operation effectively relieved the Customer's technology – the process of starting the production of the liquid is reduced to two clicks on the industrial computer operating the machine.
The repeatability of the liquid production process eliminated the costs associated with production errors – there are no defective batches of the liquid production and the ease of starting the production process allowed quick training of the service, thanks to which the Customer can finally go on a deserved vacation 🙂
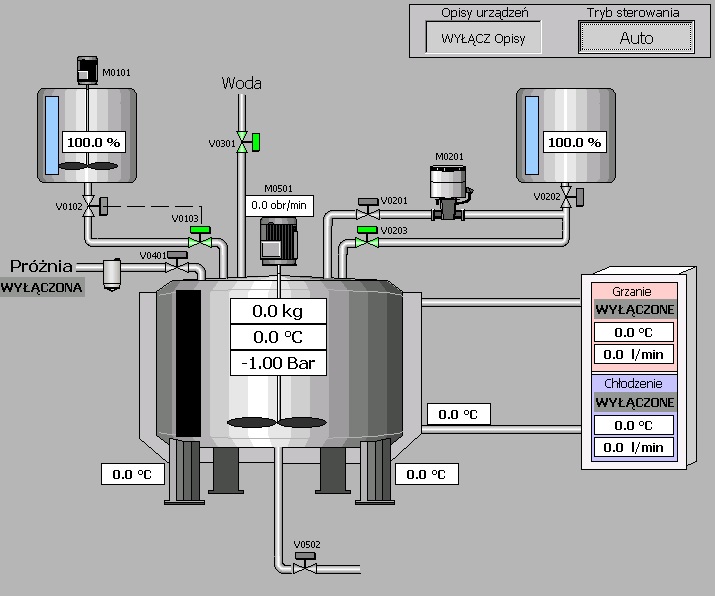
Comprehensive support of the production plant
Customer turned to us with an urgent need – system he was using lost support and the architecture it was developed in (MS Access) prevented from stable work in a network environment. The original vision of the system was successfully completed in a relatively short time. Over time, and with the use of the system, in the Customer's mind new ideas of expanding its functionality started to emerge.
The system was developed according to the SCRUM methodology – the Customer could constantly run a stable product, and subsequent versions extended the capabilities of the system. Our activities were mainly remote, which allowed us to optimize the cost of the task and save time. Gradually, we were adding new modules and functionalities. In addition, we integrated this system with weighing and labeling systems and we provided a function to read data from multiple sensors on the production line.
Operation of the production supervision system: at the stage of adding a new order, the system is able to properly recalculate necessary raw materials, available stock levels, expiration dates and other predefined parameters. The report module allows for a detailed analysis of the entire production process, thus helping to eliminate any production errors that may occur. Statistical data are used by the company's management: cross-sectional view of costs, assessment of the scale of cooperation with customers and quality of supply allows to make strategic decisions necessary for the development of the Plant.
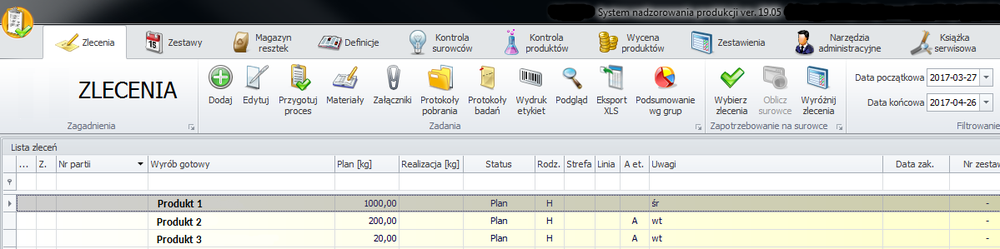
Today, the system provides continuous control of the entire production process from the moment of warehouse reception, through all stages of processing and storage, up to the point of the release and invoicing of the final product. It supports the daily work of purchasing, quality control, production and storage departments.
As a result, the Customer gained a reliable operating system developed according to requirements, and Tewemo gained trust of another satisfied Customer and a well-executed project, which is a model for next versions of the "Production Supervision System".